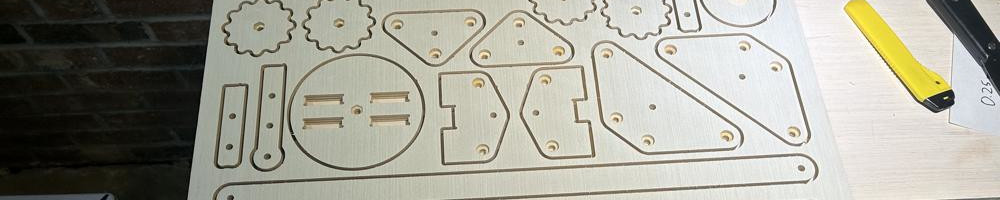
CNC Camera Arm
With a desire to film more projects, and an itch to test out the latest MPCNC reincarnation, I designed and machined a large camera arm based on an architect lamp.
With a desire to film more projects, and an itch to test out the latest MPCNC reincarnation, I designed and machined a large camera arm based on an architect lamp.
I have been thinking about this project for a long time. After I started using the needle cutter, I really wanted a vacuum table that could flatten the foamboard, and an underlying work surface that would not destroy the cutting tool.
After a two week hiatus from the MPCNC, I got the itch to get back to making things. I wanted to salvage the spoilboard as much as I could, level it out, and create a few clamps to make workpiece holding a little easier.
After a few years of rebuilds, teardowns, and tool changes, I am finally adding a router to my MPCNC. I have been wanting to work more with sheet material like wood, acrylic, and even aluminum if I can get the hang of using this tool.
After a hiatus, I decided to revisit the needle cutter and get back to making planes from the free svg plans on FliteTest. I wanted to characterize the performance of the MPCNC and develop a streamlined workflow for creating parts that would fit together snug without being too tight.
In my pursuit of speeding up my RC plane building, I found a new tool on the Flite Test forums, a needle cutter. This is a simple tool where a flexible piece of music wire is attached to a brushless motor to repeatedly puncture soft materials. When these punctures are spaced close enough, it acts as a cutting tool.
There seems to be a proliferation of inexpensive diode lasers available from overseas ranging from 1 to 15 W. It is somewhat concerning that someone can purchase such a high powered blinding device so easily. It is also very tempting…
Now that the MPCNC is assembled and wired up, it’s time to make something! I decided to start with some simple actions with a pen plotter and vinyl cutter.